How a Global E-Commerce Retailer Optimized Trailer Unloading with Rightbot's Wolverine
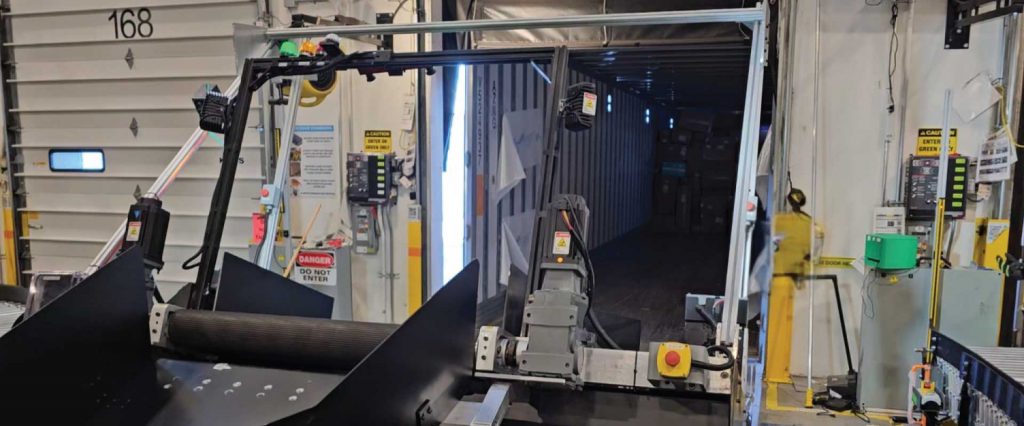
Customer Overview
As one of the world’s top e-commerce retailers, this customer operates a massive supply chain comprising a multitude of middle mile sortation centers, fulfillment centers, and last-mile delivery hubs across North America. With a relentless focus on efficiency and automation, the customer continuously seeks to enhance its logistics operations. Given the e-commerce supply chain is almost 100% floor loaded, manual unloading of trailers and containers across its supply chain is one of the most labor-intensive and time-consuming processes for the customer, and therefore has been a focus for automation. They had found it difficult to automate this process effectively— until now.
The Challenge
The customer had been seeking and evaluating solutions across the board to automate its middle mile sortation unloading operations. However, none of the existing solutions could meet their requirements:
1. Throughput Required: Given the high volume and focus on customer delight, the customer needed a solution which could unload at >1000 unloads/hour. During peak season, this requirement could go up to 1500 unload/hr. No robotic solution could deliver such speeds
2. Highly Unstructured Stacking: The middle mile sortation centers received final customer orders – These were highly unstructured goods stacked and piled inside trailers – similar to parcels and couriers. Despite tall claims, no robotic solution has been able to handle such unstructured goods.
Trailers/ containers varied from very well structured, few SKUs to highly unstructured, multiple SKUs.
3. Non-Conveyable Goods: A large percentage of their orders consist of large items, larger than 37 inches or heavier than 50 lbs, also termed as “non conveyables” (since they can’t be handled by typical conveyor systems). These include TVs, printers, and
strollers to name a few. No robotic solution was able to handle these.
4. Huge Variability of Goods: Typical to parcels, couriers or e-commerce orders, the goods were HIGHLY variable. The same trailer would contain boxes, non-conveyables (as mentioned above), pouches, thin parcels and flats, or even irregular shaped items like cylindrical tubes. None of the existing solutions could handle such variability.
The Solution
Rightbot’s Wolverine was introduced at the retailer’s middle-mile sortation centers. Wolverine was able to integrate with a flex conveyor as well as the existing telescopic conveyor, and was able to seamlessly unload every good which came in any of the trailers.
Results & Impact
The key outcomes included:
– For trailers with small to medium-sized goods, Wolverine achieved an impressive 3500+ unloads per hour, with a peak productivity of 7000 unloads/hr achieved.
– For trailers with a high percentage of non-conveyables , Wolverine delivered an average productivity of 2000+ unloads per hour.
– Trailers unloaded 2-3 times faster than manual operations (with 2 operators unloading)
Conclusion
Rightbot’s Wolverine proved its ability to tackle the most complex trailer unloading challenges with unmatched speed and efficiency. Whether dealing with large, irregular, or non-conveyable goods, Wolverine provides a seamless, fully automated, and highly productive unloading solution.
Are you facing similar issues in your trailer unloading operations and want to see how Wolverine can help you eliminate these challenges? Contact us now to learn more!